No one needs to remind Houston homeowners of the impact inflation is having. Anyone who shops for groceries is fully aware of its effect, as are many grumbling gas station patrons. You would expect that Houston real estate would be among the affected categories—and although that is true, it’s clear there is more than just inflation going on.
If February’s official 7.87% inflation figure is accurate, Reuter’s February calculation of a 15% rise in the median U.S. home’s purchase price clearly reflects other factors. There IS a supply-demand imbalance at work, for sure, as the latest inventory figures continue to confirm. But the magnitude of the price escalation points to yet another contributing factor.
One likely candidate is contributing to the sluggish introduction of new housing units. The press has settled on calling this the “supply chain” issue—a witch’s brew of logistical snags that American consumers and producers are now learning to cope with. For the first time since the end of World War II, shortages in a growing list of the goods and materials that go into home building and improvements are postponing completion dates. Examples:
• Appliances. In a panel discussion at last week’s International Builders’ Show, the CEO of the National Association of Home Builders pointed to one extreme case where a builder’s appliance supplier told him not to expect deliveries for a specific house “for up to 12 months.” More typical are delays of a month or two—yet the cost across the nation as a whole is significant. Reasons given are chip shortages, labor shortages, factory lockdowns, and the catch-all “logistical challenges.”
• Windows and Doors. Businessobserver.com reports that 63% of homebuilders cited windows as their biggest material shortage last year. Labor shortages on the docks and among truck drivers who transport goods when they’re unloaded from ships contribute to slow deliveries of imports.
• Trusses. Roof trusses are said to be about 10 weeks behind in production.
• Ductwork. Lead times for HVAC equipment and repair components “have increased three to four times” their normal delivery backlog, according to last week’s Air Conditioning Heating and Refrigeration News.
The effects are nearly universal across America, causing the NAHB to report that more than 90% of builders reported delays and materials shortages last year. With the government’s Producer Price Index for construction having already climbed by 22% in 2021—and with items like softwood lumber prices having spiked almost 24% in December alone, it’s small wonder that Houston listing prices are unlikely to decline anytime soon—or that many of today’s prospective buyers expect that today’s prices may look tame someday soon. For an update on how your own Houston real estate plans might fit in with the current active Houston market, do give us a call! Rinnovare Realty, LLC (832) 445-4957 or visit us at: www.rinnovarerealty.com .
Main Header
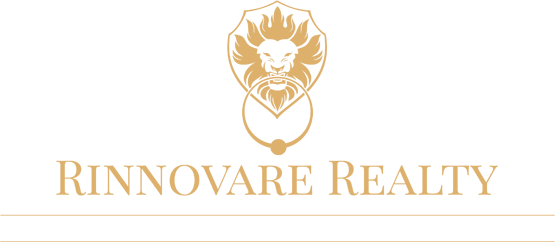
Join Our Vip List
Main Content
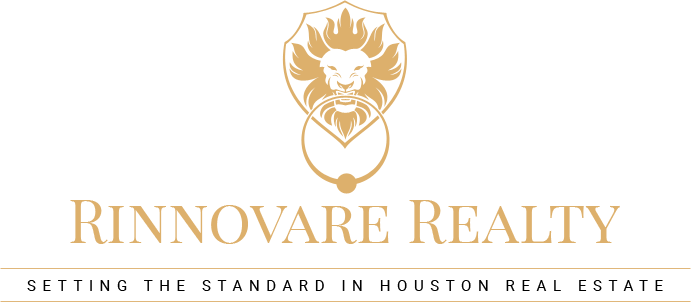
Home » Houston Supply Chain Issues add to Inflation Effect